A dependable source of quality parts supply is critical to maintain safe, reliable, and profitable operation of industrial facilities. However, aging equipment and pressure on the global supply chain have created a challenging environment in the replacement parts.
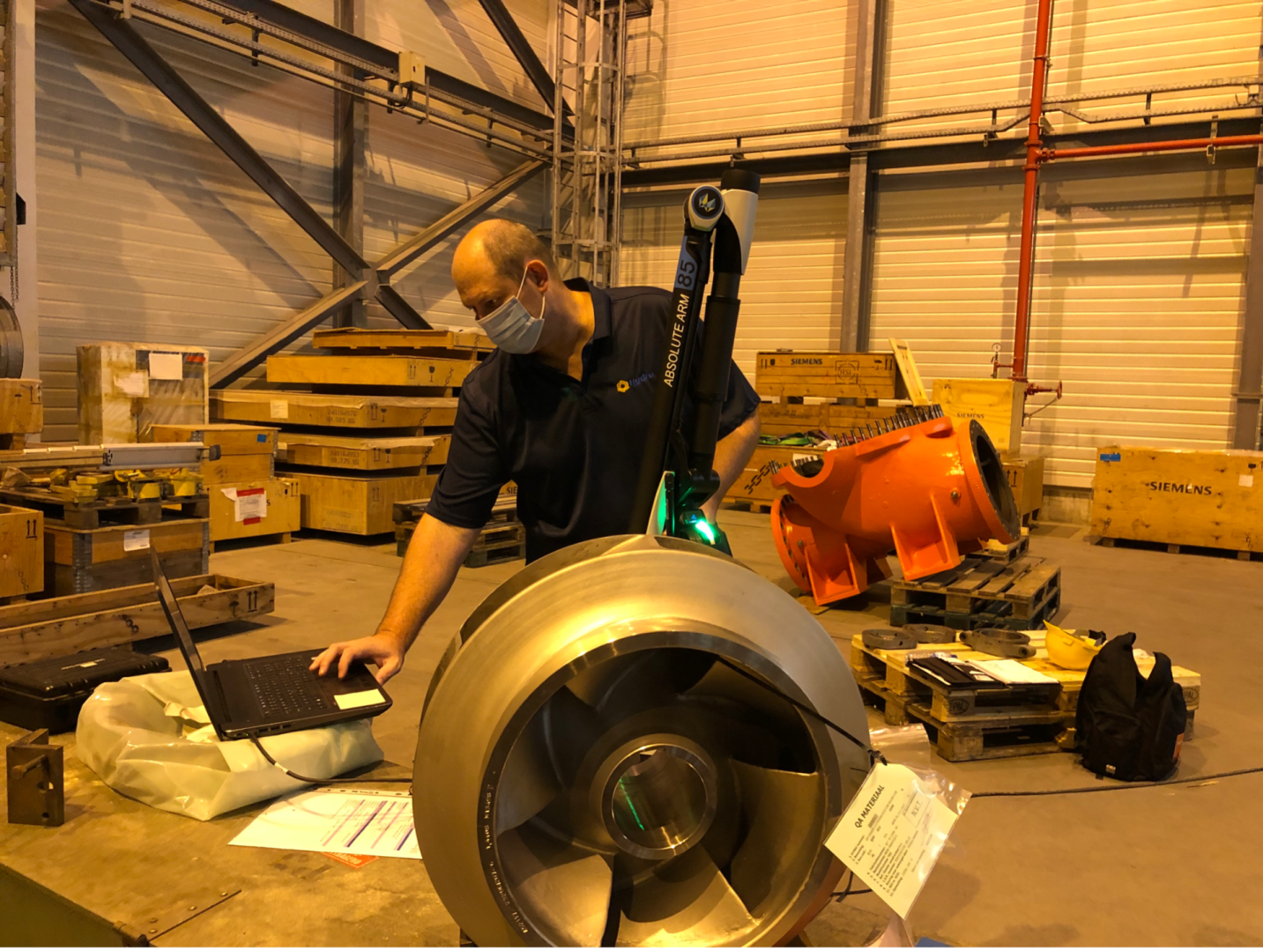
Obsolescence and loss of supplier experience have resulted in many plants rethinking the idea that the original equipment manufacturer (OEM) should be the go-to source for parts supply. Consolidation of OEMs and retirement and down-sizing on the supplier side have led to loss of capability, compromised quality, and slower response times. Ordering parts through the OEM is also a highly transactional process that rarely engages engineering. Without engineering involvement, there is no opportunity to determine if new technology or design improvements are available that can improve the reliability of the component.
Hydro helps end users meet the challenges of obsolescence with hard-earned reverse engineering expertise, an extensive library of parts drawings across OEMs, a global engineering network, and a dedicated parts division that delivers industry-leading turnaround times for cast components.
When sourcing an alternative for quality parts, it is important to understand that reverse engineering goes beyond simple replication and must engage an experienced engineering team. Advanced technologies can help significantly in the process of reverse engineering critical parts, but relying on these technologies alone is not enough to ensure proper design and manufacture. Geometry, metallurgy, hardness, tolerances, and coatings should all be considered and they add to the complexity of the reverse engineering process. Reproducing the part without reviewing the hydraulic, mechanical, and material characteristics of the component can lead to incorrect geometry or failure of the part when placed in service.
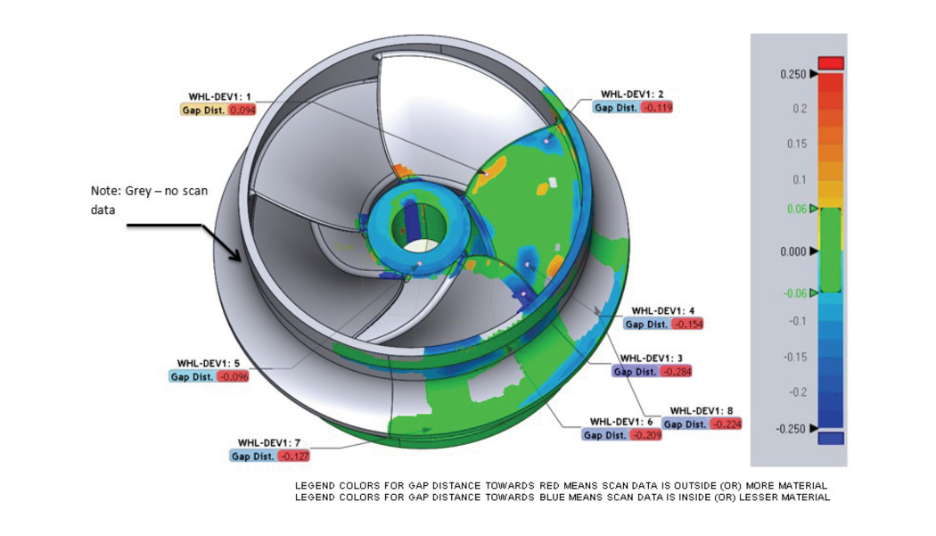
Hydro’s reverse engineering procedures ensure that a comprehensive engineering review is completed during the reverse engineering process. We are also able to leverage our library of known failure mechanisms and proven solutions to improve component design and performance.
Read about how Hydro helps end users overcome the challenges of obsolescence and other supply chain challenges in our case studies with Nuclear Engineering International here and here.
Discover our Hydro’s Parts Solutions division here.