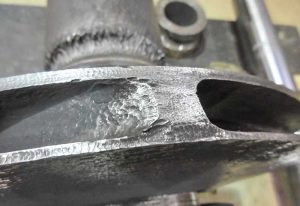
Damaged impeller showcasing severe corrosion.
A major steel plant on the East Coast had been experiencing catastrophic failures with its five-stage descaling pumps. The plant operated using three multistage axially split (BB3) pumps with two spares. All five of the pumps had a mean time between repair (MTBR) of two years. In this case, the plant water quality was considered to be less than ideal, and the entrained abrasives were a factor contributing to the repeated failures.
Poor water quality can lead to a number of pump reliability issues. When pumping fluids with abrasive material, pumps experience erosion and corrosion, and the effects can rapidly degrade both the casings and critical inner elements. While erosion and corrosion alone are not always a difficult problem to solve, it is important to have a firm understanding of the relationship between various types of erosion and corrosion and the metallurgy used in designing the pumps.
Further analysis showcased excessive clearances and inconsistencies with component fits that also contributed to pump performance degradation outside the abrasion. In order to increase the MTBR of the pumps at the plant, the aftermarket pump service provider recommended several engineered upgrades including new impellers to be manufactured using advanced mold technology, specifically addressing the surface finish and dimensional consistency.
Source: https://www.pumpsandsystems.com/maximizing-efficiency-descaling-pumps